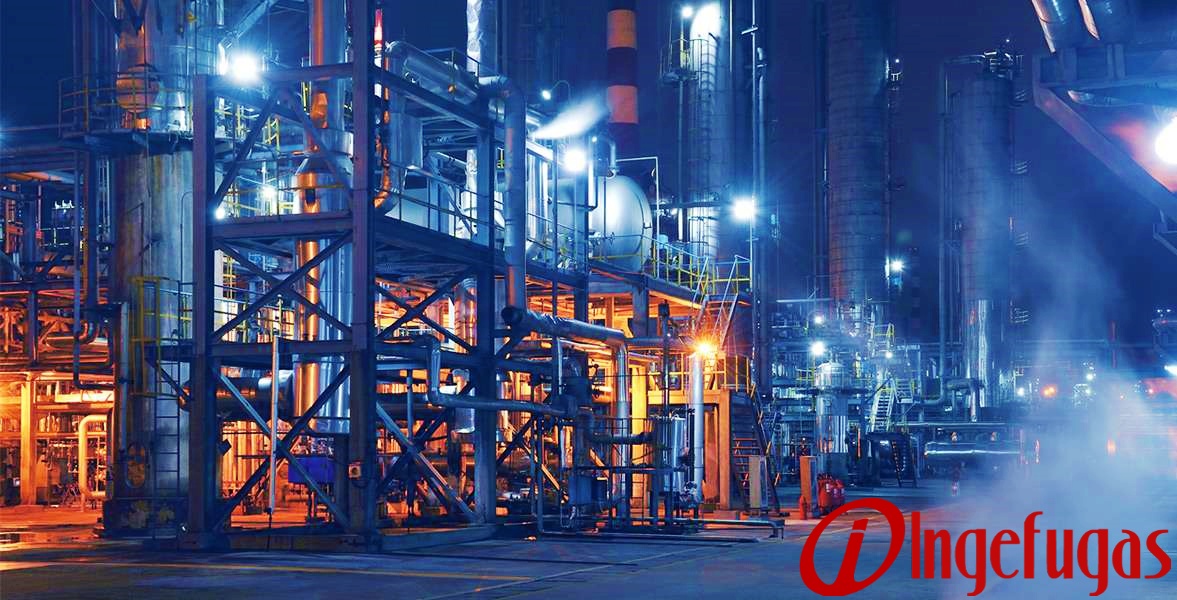
Imagina que trabajas con un equipo ATEX en un entorno industrial y, de repente, un fallo inesperado detiene la producción. No solo se pone en riesgo la seguridad de la planta, sino que cada minuto de inactividad significa pérdidas económicas. Además, una interrupción inesperada puede afectar la confianza del equipo de trabajo y generar retrasos en la cadena de producción.
Los fallos técnicos en equipos ATEX pueden parecer inevitables, sin embargo, muchos de ellos pueden prevenirse con el conocimiento y las estrategias adecuadas. Por esta razón, identificar los problemas más comunes y saber cómo evitarlos es clave para garantizar la seguridad y el rendimiento óptimo de estos equipos.
Sin un mantenimiento adecuado y una supervisión constante, los problemas mecánicos, eléctricos y de calibración pueden convertir un equipo ATEX en una amenaza latente. Pero la buena noticia es que existen soluciones efectivas que pueden ayudarte a evitar estos problemas y garantizar la seguridad y eficiencia operativa de tu empresa.
¿Qué tipo de fallos técnicos son más frecuentes en equipos ATEX?
Los equipos ATEX están diseñados para operar en atmósferas explosivas con seguridad, pero eso no significa que sean inmunes a fallos técnicos. A continuación, analizamos los más frecuentes y cómo pueden afectar tanto la seguridad como la productividad.
1. Fallos relacionados con la protección
- Pérdida de estanqueidad: Cuando las juntas o sellos fallan, pueden permitir la entrada de sustancias explosivas dentro del equipo.
- Deterioro de la protección contra explosiones: Factores como la corrosión y el desgaste pueden comprometer la seguridad del equipo.
- Fallas en los sistemas de seguridad intrínsecos: Problemas en barreras de seguridad o circuitos de protección pueden hacer que los dispositivos pierdan su capacidad de operar en zonas ATEX.
📌 Para evitar estos problemas, es fundamental realizar inspecciones periódicas y asegurarse de que los materiales utilizados sean resistentes a las condiciones del entorno.
2. Problemas mecánicos
- Desgaste excesivo de componentes móviles: Puede generar chispas por fricción, lo que aumenta el riesgo de ignición.
- Desalineación de piezas rotativas: En equipos como bombas o motores, puede aumentar la probabilidad de fallos.
- Fallas en sistemas de lubricación: El sobrecalentamiento y la fricción excesiva pueden provocar riesgos innecesarios.
📌 En este caso, implementar programas de mantenimiento predictivo ayuda a detectar desgastes y desajustes antes de que se conviertan en problemas graves.
3. Fallos eléctricos
- Cortocircuitos: Pueden generar arcos eléctricos o sobrecalentamiento en equipos críticos.
- Fallas en el aislamiento: La degradación del aislamiento puede provocar chispas o descargas eléctricas.
- Problemas en conexiones a tierra: Las malas conexiones pueden aumentar el riesgo de descargas electrostáticas peligrosas.
📌 Por lo tanto, es recomendable realizar inspecciones regulares del cableado y utilizar siempre materiales certificados para ambientes ATEX.
4. Errores de calibración y control
- Desajustes en sensores de temperatura: Pueden llevar a sobrecalentamientos peligrosos en zonas sensibles.
- Fallos en sistemas de control: Un error en la programación o calibración de equipos puede hacer que funcionen fuera de los parámetros seguros.
📌 En consecuencia, es imprescindible implementar protocolos de calibración y pruebas periódicas de los sistemas de control.
5. Problemas de mantenimiento
- Acumulación de polvo o suciedad: Puede causar sobrecalentamiento o interferir con los sistemas de protección.
- Reemplazo incorrecto de componentes: El uso de piezas no certificadas puede comprometer la seguridad del equipo.
📌 Para evitar estas complicaciones, es clave establecer un plan de mantenimiento riguroso y asegurarse de que las piezas de repuesto sean siempre certificadas para entornos ATEX.
Cómo evitar fallos en equipos ATEX y garantizar la seguridad operativa
Si bien los fallos técnicos pueden representar un gran riesgo, la clave para evitarlos es la prevención y el mantenimiento adecuado. A continuación, te mostramos algunas estrategias recomendadas:
✔ Realizar inspecciones frecuentes: Revisar el estado de los sellos, conexiones y sistemas eléctricos.
✔ Capacitar al personal: Asegurar que los operadores conozcan los riesgos y cómo prevenirlos.
✔ Implementar sensores de monitoreo: Utilizar sistemas que detecten variaciones en la temperatura, vibración y presión.
✔ Utilizar solo equipos y repuestos certificados: La certificación ATEX es crucial para garantizar el cumplimiento normativo y la seguridad.
Por lo tanto, evita problemas antes de que ocurran
Los fallos en equipos ATEX no solo afectan la productividad, sino que también pueden comprometer la seguridad de toda la operación. Por esta razón, la prevención es tu mejor herramienta para evitar riesgos innecesarios y garantizar un entorno seguro y eficiente.
Un solo fallo en un equipo ATEX puede poner en riesgo la seguridad de tu operación, detener la producción y generar costos inesperados. Lo que hoy parece un pequeño desperfecto, mañana podría ser la causa de un incidente grave.
Imagina el impacto de un fallo técnico en plena actividad: una chispa donde no debería haberla, una conexión deteriorada que pasa desapercibida o un sensor descalibrado que no detecta un problema a tiempo. No solo sería una amenaza para tu equipo y tu infraestructura, sino también para la seguridad de quienes trabajan en estos entornos.
La buena noticia es que estos riesgos se pueden evitar con información fiable y un enfoque preventivo. No dejes que la falta de mantenimiento se convierta en un problema irreversible.
Mantente informado con nuestra sección de noticias, donde encontrarás artículos y guías sobre seguridad en atmósferas explosivas. Si no encuentras la información que necesitas, contáctanos y resolveremos tus dudas con el conocimiento que nos respalda.
Preguntas frecuentes sobre fallos técnicos y mantenimiento de equipos ATEX
¿Cómo se pueden prevenir los fallos técnicos en los equipos ATEX?
Prevenir fallos en equipos ATEX requiere una combinación de mantenimiento proactivo, inspecciones regulares y el uso adecuado del equipo. Por ejemplo, algunas estrategias clave incluyen:
✔ Realizar revisiones periódicas para detectar signos de desgaste o corrosión.
✔ Calibrar los sistemas de control para evitar desajustes que comprometan la seguridad.
✔ Capacitar al personal en el uso adecuado y el reconocimiento de señales de advertencia.
✔ Utilizar solo repuestos certificados para garantizar el cumplimiento con normativas ATEX.
📌 Mantenerse informado y seguir protocolos estrictos puede evitar problemas antes de que ocurran.
¿Qué impacto tienen los fallos técnicos en la seguridad de los trabajadores en entornos ATEX?
Los fallos técnicos en equipos ATEX pueden ser críticos para la seguridad, ya que aumentan el riesgo de incendios, explosiones y accidentes industriales. Entre los impactos más peligrosos están:
- Riesgo de ignición: Un fallo eléctrico o mecánico puede generar chispas o sobrecalentamiento en atmósferas explosivas.
- Fugas de sustancias peligrosas: Una falla en la estanqueidad puede permitir la liberación de gases inflamables.
- Exposición a descargas eléctricas: Problemas de aislamiento o conexión a tierra pueden generar peligros eléctricos.
📌 Un programa de mantenimiento preventivo reduce significativamente estos riesgos, protegiendo a los trabajadores y asegurando un entorno seguro.
¿Qué tipo de mantenimiento regular es necesario para evitar fallos técnicos en equipos ATEX?
El mantenimiento regular de equipos ATEX debe incluir inspecciones programadas, monitoreo continuo y pruebas funcionales. Además, una planificación adecuada puede evitar imprevistos y prolongar la vida útil del equipo. Para ello, se recomienda seguir estas prácticas:
- Realizar inspecciones visuales frecuentes para detectar signos de daño, corrosión o acumulación de suciedad. De esta manera, es posible actuar antes de que un problema menor se convierta en una falla crítica.
- Llevar a cabo pruebas eléctricas y de aislamiento para asegurar que no haya fugas de corriente o puntos de ignición. Por lo tanto, estas pruebas son esenciales para reducir riesgos en zonas ATEX.
- Lubricar y ajustar las piezas móviles para evitar desgaste prematuro. En consecuencia, esto previene fricción excesiva que podría generar chispas o sobrecalentamiento.
- Verificar sensores y sistemas de control para garantizar que operen dentro de parámetros seguros. Así, se evita que pequeños desajustes deriven en fallos mayores.
📌 En definitiva, una estrategia de mantenimiento bien planificada no solo minimiza riesgos, sino que también optimiza la eficiencia y seguridad de los equipos ATEX.s.
¿Cuáles son las consecuencias de un fallo técnico en un equipo ATEX?
Las consecuencias de un fallo en un equipo ATEX pueden variar desde costos operativos elevados hasta accidentes industriales graves. Algunos escenarios incluyen:
- Pérdidas económicas: Un equipo fuera de servicio puede afectar la producción y generar gastos inesperados.
- Accidentes laborales: Un fallo puede comprometer la seguridad de los trabajadores y del entorno.
- Multas y sanciones regulatorias: El incumplimiento de normativas ATEX puede derivar en sanciones legales.
📌 Invertir en prevención y mantenimiento es clave para evitar estas consecuencias y garantizar operaciones seguras.
¿Qué factores contribuyen a los fallos técnicos en los equipos ATEX?
Los fallos técnicos en equipos ATEX pueden ser causados por diversos factores, entre ellos:
- Mantenimiento deficiente: No realizar inspecciones y revisiones periódicas.
- Condiciones ambientales adversas: Humedad, polvo o sustancias corrosivas pueden degradar los componentes.
- Sobrecarga eléctrica: Exceso de voltaje o fallos en la conexión a tierra pueden causar fallos eléctricos.
- Uso inadecuado del equipo: Operar fuera de los parámetros recomendados aumenta el riesgo de fallos.
📌 Entender estos factores permite implementar estrategias de prevención más efectivas y reducir riesgos operativos.